Real-Time Production Management and Control
The manufacturing execution system VMP Plan, integrated with the Cegid Primavera ERP, enables full management of the production cycle in a completely integrated manner, eliminating the most time-consuming and low-value tasks. This software covers all production processes, from Product Creation, Raw Material Procurement, Budgeting, Production Planning, and Subcontracting, to the Shipment of the Final Product.
Automate Production Processes with VMP Plan
VMP Plan is a robust solution for production management and control across various industries, enabling process automation, waste reduction, and real-time monitoring. The software is adaptable to industries such as textile, metalworking, footwear, packaging, and others, optimizing every stage of the production cycle.
Furthermore, it enables efficient resource management, offering centralized access to all available resources, from materials to equipment and human resources. You will have the ability to fully visualize the entire production cycle.
In order to maximize your capabilities and optimize resource utilization, the VMP Plan offers extensive functional coverage that assists in streamlining your production process. It helps improve response times and reduces costs associated with downtime. Through a simple and intuitive graphical interface, effective control of your production process is in your hands.
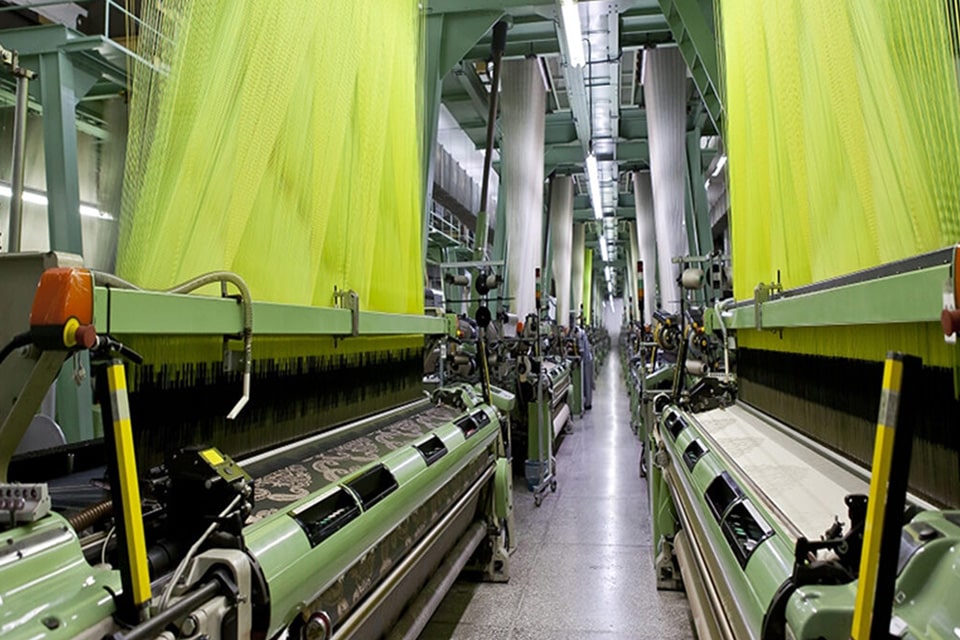
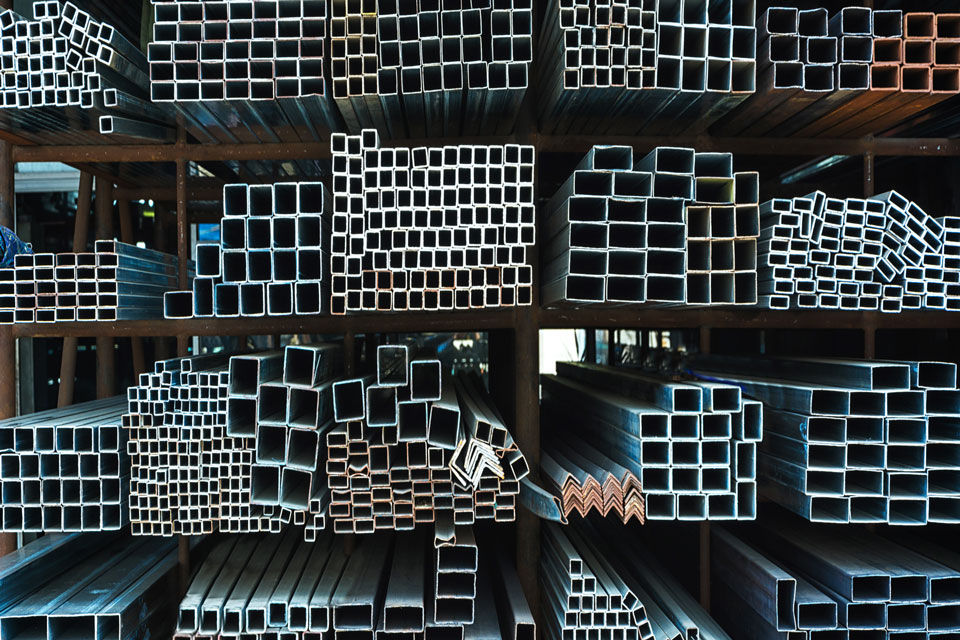
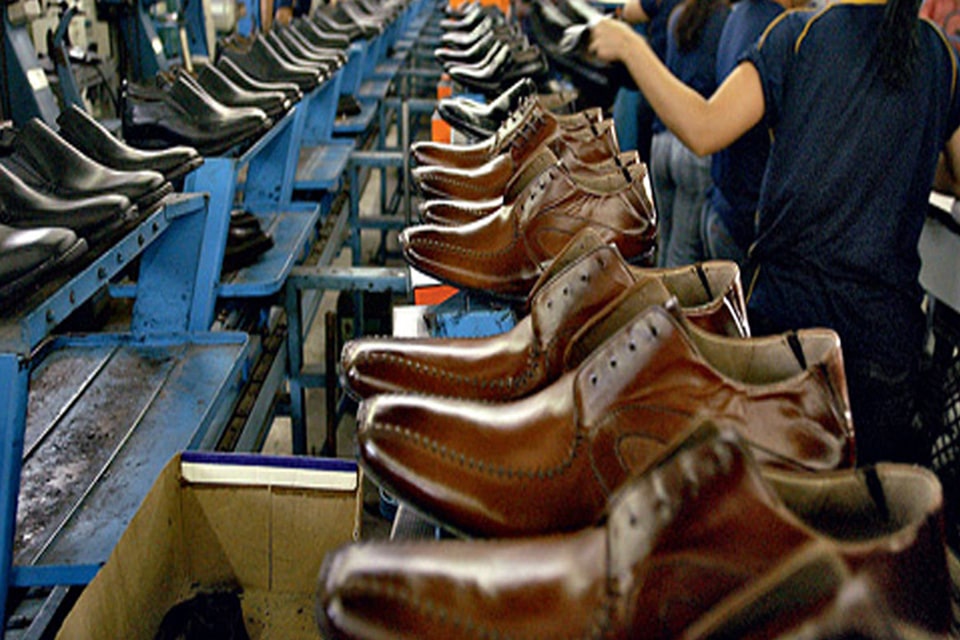
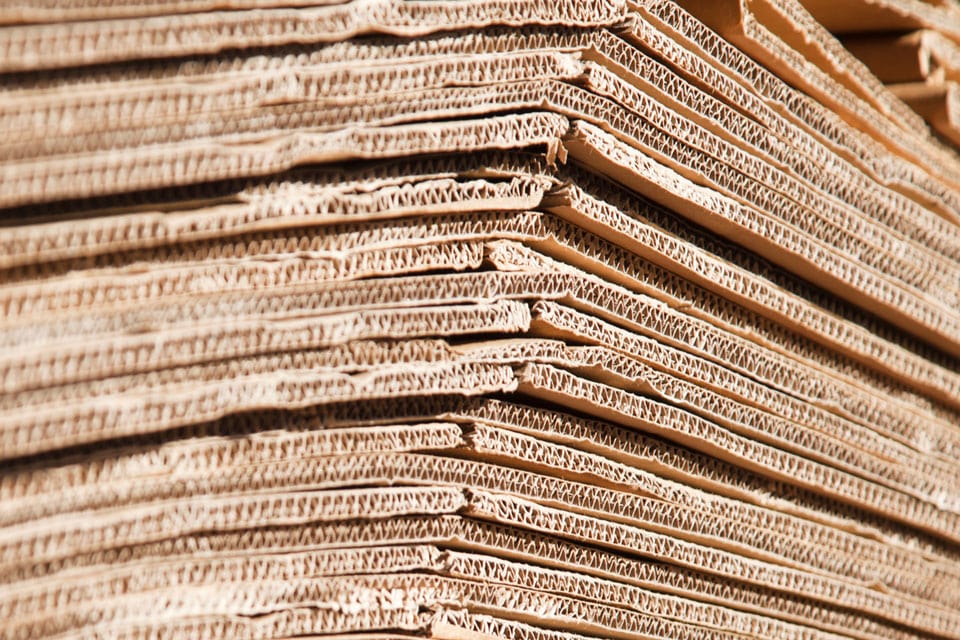
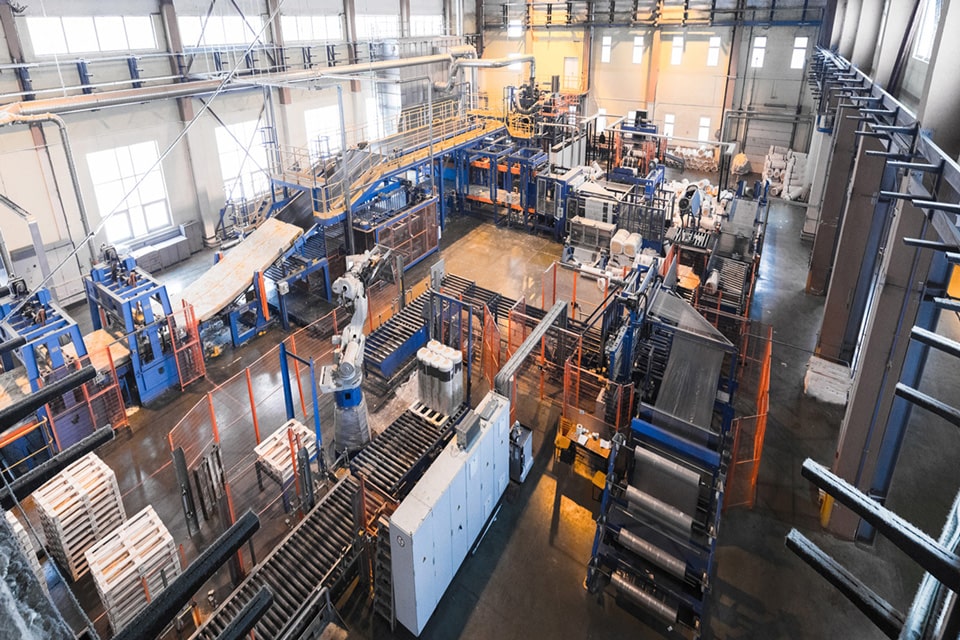
Real-time production planning and control
Subcontractor reception, procurement and management
Quick creation of articles and fact sheets
Complete and integrated management of the entire organization
Specific modules for different industries
Real-time information collection on the shop floor
Quality control throughout the production process
Customizable according to the needs of each business
Assisted product shipping
Graphical analysis of production and profitability
main features
Assisted Creation of Articles / Technical Sheet
- Digitization of all product information
- Visualization in a hierarchical tree with technical data integration for sub-products
- Article creation assistant with unlimited encoding parameters
- Automatic expansion of components from the model for all colors, sizes, or measurements
- Definition of customer and supplier references associated with system articles
- Technical data sheet without limits on materials and operations
- Certification control - GOTS, OEKO-TEX, BCI, EUROPEAN FLAX, etc.
- Importation from modeling software
Product Development
- Management and control of sample execution
- Digitization of all sample information exchange and documentation
- No need to create an article
- Clients or potential clients
- Multiple execution and control scripts
- Unlimited and user-configurable operations/steps
- Cost and time recording per operation
- Automatic email notification upon operation execution
Budgeting
- Creation of budgets and price lists
- Budget creation without the need to create articles
- Unlimited templates for Excel calculations
- Communication between the database and Excel
- Budgets with version tracking and approval control
- Commission grids by seller, brand, customer, etc.
- Definition of commissions for automatic calculation
- Prices based on dimensions (colors, sizes, etc.) and ranges
- Simulation for production quantities
- Attribute transfer to the article sheet
Manufacturing Orders
- Order placement for manufacturing in various modes (automatic, grouped, ungrouped)
- Manufacturing orders without a specific order
- Utilization of ongoing productions and/or stock
- Verification of fulfilled orders
- Calculation of customer tolerance and/or article waste
- Printing with various formats and article images
Needs Calculation
- Requirements for multiple manufacturing orders
- Calculation with various parameters: current and minimum stock, supplier requisitions, operations, and warehouses
- Automatic creation of component requisitions
- Suggestion of regular supplier and last purchase price
- Reservation of materials for manufacturing order
Graphic Planning
- Planning view in Gantt chart or grid
- Internal or subcontracted planning
- Fitting suggestion by delivery date or execution time
- Planning alteration through drag & drop
- Load analysis with excess alert
- Industrial calendar with exception possibilities
- Automatic planning using various criteria:
- Customer delivery deadlines
- Execution times at each workstation
- Capacity factors and schedules
- Exceptions for workable hours and capacity
- Among others
Manufacturing Plans
– Manufacturing Scheduling
– Suborder for one or more operations in manufacturing
– Internal or subcontracted execution
– Automatic service request with suggested price
– Modification of quantities to be produced
– Add, remove, or replace components
– Aggregation of operations
– Cadence and delivery deadline
– Operation, composition, and component observations
Movement - Material Entry
– Analysis of pending material delivery
– Assisted material entry
– Automatic suggestion of warehouse and lot if needed
– Barcode/QR Code reading
– Label printing
– Possibility of mobile reception
Movement - Shipment
– Assisted shipment, segmented by production sector
– Shipment to internal or subcontracted production
– Possibility of material preparation
– Automatic issuance of certified goods tracking document (external production)
– Barcode/QR Code reading
Movement - Floor Factory Reception / Execution
– Subcontracting Reception/Return Movement
– Internal Execution
– Recording of times and quantities produced
– Setup, Start, and End of production
– Operator or group of operators identification
– Execution sorting according to the planning
– Different layout per section
– Visualization of all documentation in the technical data sheet
Production Monitoring
– Production status dashboards
– Real-time production monitoring
– Quantities and percentage completed and outstanding by sector
– Materials sent and consumed
– Product traceability
Quality Control
– Flexibility in configuring quality tests
– Segmentation of tests to be registered by families, brands, etc.
– Definition of the collection times for each test or test group, under customizable conditions
– Parameterization and customization of factors that approve or reject each test
Packing List and Picking
– Pre-Packing: Automatic and/or manual distribution by packaging type, destinations, and dimensions
– Packing defined by the operator
– Various packings per order
– Automatic label creation
– Customization of packing and labels per customer
– Shipment from picking
– Calculation of volume and weight
Procedures
– Process management, such as samples, complaints, product engineering, among others
– Typed processes linked to articles, documents and budgeting
– Customization of scripts and association to each process
– Customization of possible states for each step of the scripts
– Email notifications regarding the change of status of a certain process step
– Documentary repository for each process or step within the process script
Information Exploration
– Production status analysis
– Cost analysis
– Product traceability
– Article statement and inventory by manufacturing order
– Identification of components consumed throughout the production process
– Custom dashboards