Automate Production in the Metalworking Industry with VMP Plan
Companies in the metalworking sector are constantly faced with the need to optimize processes to enhance competitiveness and profitability. VMP Plan, integrated into Cegid's ERP v10, is a comprehensive vertical management solution that encompasses the entire organization, from production to top-level management.
VMP Plan promotes comprehensive management of the production cycle in a fully integrated way, eliminating the most time-consuming and lower value-added tasks. It encompasses all production processes in the metalworking industry, such as:
– Product Development
– Needs Calculation
– Quality Control
– Etc.
This solution results from over 35 years of experience in various sectors, incorporating a set of standard processes coupled with flexibility that allows adapting the VMP Plan to the specific needs of each organization.
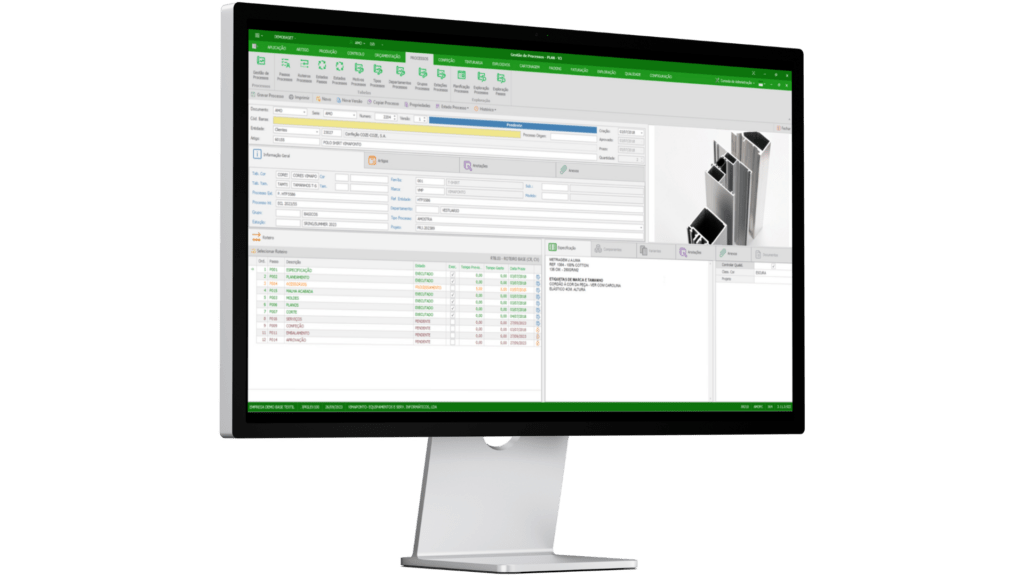
main features
Product Development
– Management and control of sample execution
– No need to create an article
– Customers or potential customers
– Various execution and control workflows
– Unlimited and user-configurable operations/steps
– Cost and time recording per operation
– Automatic email notification upon operation completion
– Sample documentation repository
Budgeting
- Creation of budgets and price lists
- Budget creation without the need to create articles
- Unlimited templates for Excel calculations
- Communication between the database and Excel
- Budgets with version tracking and approval control
- Commission grids by seller, brand, customer, etc.
- Definition of commissions for automatic calculation
- Prices based on dimensions (colors, sizes, etc.) and ranges
- Simulation for production quantities
- Attribute transfer to the article sheet
Assisted Article Creation
– Guided article creation
– Automatic attribute suggestion
– Graphic exploration of the composition of the article
– Technical sheet with unlimited operations and levels
– Combination of technical sheets
– Clear definition of the manufacturing process
– Production alternatives
– Attached images and files
Manufacturing Orders
- Order placement for manufacturing in various modes (automatic, grouped, ungrouped)
- Manufacturing orders without a specific order
- Utilization of ongoing productions and/or stock
- Verification of fulfilled orders
- Calculation of customer tolerance and/or article waste
- Printing with various formats and article images
Needs Calculation
– Requirements by manufacturing orders or orders
– Calculation with various parameters: current and minimum stock, supplier requisitions, operations, and warehouses
– Automatic component requisition
– Usual supplier suggestion
– Material reservation for manufacturing order
Graphic Planning
- Planning view in Gantt chart or grid
- Internal or subcontracted planning
- Fitting suggestion by delivery date or execution time
- Planning alteration through drag & drop
- Load analysis with excess alert
- Industrial calendar with exception possibilities
- Automatic planning using various criteria:
- Customer delivery deadlines
- Execution times at each workstation
- Capacity factors and schedules
- Exceptions for workable hours and capacity
- Among others
Movement
– Permanent inventory
– Material preparation
– Automatic issuance of certified goods tracking document
– Movement executed by operators
– Visibility and recording by subcontractors
– Material return
Quality Control
– Flexibility in configuring quality tests
– Segmentation by families, brands, etc.
– Definition of test collection moments
– Parameterization and customization of factors that approve or reject tests
Packing List and Picking
– Pre-Packing: Automatic and/or manual distribution by packaging type, destinations, and dimensions
– Packing defined by the operator
– Various packings per order
– Automatic label creation
– Customization of packing and labels per customer
– Shipment from picking
– Calculation of volume and weight
Information Exploration
– Production status analysis
– Cost analysis
– Product traceability
– Article statement and inventory by manufacturing order
– Identification of components consumed throughout the production process
– Custom dashboards
– Production status monitors